views
The aviation industry is experiencing a remarkable transformation as manufacturers strive to build aircraft that are more efficient, sustainable, and technologically advanced. At the forefront of this evolution are aerospace composites solutions—innovative materials that are reshaping the way aircraft are designed and constructed. These composites are playing a pivotal role in autonomous systems development as well, enabling lighter, stronger, and more adaptable airframes that meet the demands of next-generation aviation.
This article takes a closer look at why aerospace composites are becoming the backbone of modern aircraft design, their tooling engineering, and how they intersect with emerging technologies like autonomous systems.
What Are Aerospace Composites?
Aerospace composites are engineered materials made by combining two or more constituent materials with different properties to create a new material that outperforms its individual components. Typically, these combine fibers such as carbon or glass with resin matrices, resulting in materials with high strength-to-weight ratios, corrosion resistance, and exceptional durability.
These composites can be tailored to achieve specific mechanical properties and shapes, making them ideal for the complex structures required in aircraft manufacturing.
Advantages of Aerospace Composites in Aircraft Design
- Lightweight Yet Strong
Weight reduction is critical in aircraft design because it directly impacts fuel efficiency, payload capacity, and emissions. Aerospace composites provide significant weight savings compared to traditional aluminum or steel while maintaining or even improving strength and stiffness. This balance allows designers to create lighter aircraft that consume less fuel and have longer range.
- Design Flexibility
Unlike metals, composites can be molded into complex, aerodynamic shapes with fewer constraints. This design flexibility enables engineers to optimize airframes for performance, reducing drag and improving overall efficiency. Additionally, composites can integrate multiple functions—such as structural support and thermal insulation—reducing the need for additional materials.
- Corrosion and Fatigue Resistance
Composite materials are inherently resistant to corrosion and fatigue, two common issues that degrade metal structures over time. This characteristic reduces maintenance costs and increases the service life of aircraft components, enhancing safety and longevity.
- Compatibility with Autonomous Systems Development
Emerging autonomous aircraft rely heavily on advanced materials that support lightweight construction without compromising strength. Aerospace composites are essential in this context, as they allow the integration of sensors, wiring, and other electronic components within the airframe without adding excessive weight. This synergy between materials and technology is crucial for the efficiency and functionality of autonomous systems.
Applications of Aerospace Composites built to print
- Fuselage and Wings: Modern commercial aircraft like the Boeing 787 and Airbus A350 use composites extensively in these areas to achieve better fuel efficiency and performance.
- Rotor Blades: In helicopters and drones, composites enable lighter, stronger blades that improve maneuverability and reduce vibration.
- Interior Components: Composites are also used in cabin interiors to save weight while enhancing aesthetics and soundproofing.
- Unmanned Aerial Vehicles (UAVs): The lightweight property of composites is a significant advantage in UAV design, contributing to longer flight times and improved payload capacity.
What People Also Ask About Aerospace Composites and Aircraft Design
What are aerospace composites made of?
They are typically made of high-strength fibers like carbon or glass embedded within a polymer resin matrix.
Why are composites preferred over metals in aircraft?
Composites offer superior strength-to-weight ratios, corrosion resistance, design flexibility, and fatigue resistance.
How do composites contribute to autonomous systems development?
Composites enable lightweight structures capable of integrating sensors and electronics essential for autonomous operation.
Are all modern aircraft made from composites?
While many new aircraft incorporate composites significantly, metals like aluminum are still used in some parts for cost or performance reasons.
What challenges exist with using composites?
Challenges include higher initial production costs, complexity in repair processes, and the need for specialized manufacturing techniques.
Future Outlook
As technology advances, aerospace composites solutions will continue to evolve, becoming more affordable, versatile, and environmentally friendly. Research into recyclable composites and hybrid materials is ongoing, promising greener aviation in the future.
At the same time, autonomous systems development will push the demand for materials that support smarter, lighter, and more integrated airframes. The partnership between material science and aerospace technology is essential for next-generation aircraft that are more efficient, safe, and capable.
Final Thoughts
Aerospace composites are undeniably the backbone of modern aircraft design, offering unparalleled advantages in weight savings, strength, and flexibility. Their role extends beyond structural components, intersecting with autonomous systems to enable new aerospace possibilities.
For manufacturers, embracing composite build to print manufacturing is not just a technical choice but a strategic necessity to compete in the rapidly evolving aviation landscape. As these innovations mature, they promise to deliver aircraft that are lighter, smarter, and kinder to the planet—heralding a new era in aerospace engineering.
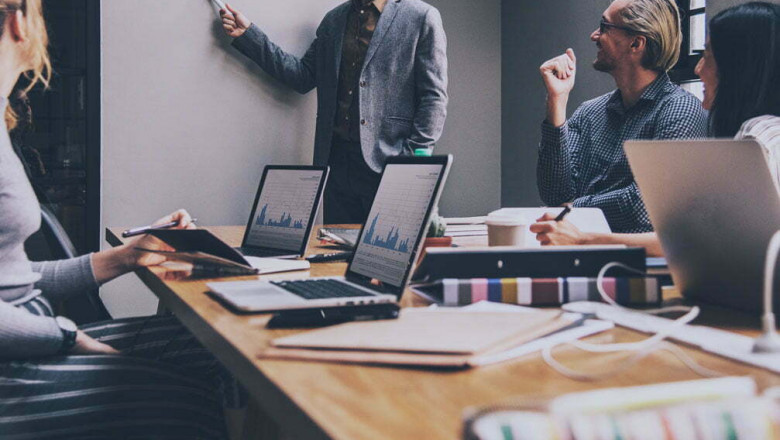

Comments
0 comment