views
Introduction to Heat Exchangers
Heat exchangers are vital additives in contemporary enterprise, facilitating thermal electricity switch among fluids to maintain operational performance and adjust temperatures throughout structures. Whether determined in chemical flowers, energy stations, refineries, or meals processing gadgets, heat exchangers make certain that power is either conserved, redirected, or controlled accurately, allowing procedures to characteristic smoothly and economically.
As business infrastructure advances toward greater sustainability and overall performance, the design and deployment of warmth exchangers have emerge as extra subtle. The demand for high-efficiency, compact, and customizable answers has by no means been better, pushing engineers and device designers to accomplice with a reliable industrial merchandise producer able to turning in tailor-made system that meets specific operational wishes.
How Heat Exchangers Work
The Principle of Thermal Transfer
The fundamental idea behind a warmness exchanger is the movement of heat from a warm fluid to a cold fluid without the 2 materials blending. This may be accomplished via strong partitions, frequently metal, which act as conductive boundaries. The process lets in electricity recuperation from waste warmth, safety of touchy components, or temperature manipulate within chemical reactions.
Depending on the layout, warmness exchangers can be used to cool or warmth fluids in a whole lot of systems. The effectiveness of a warmness exchanger relies upon on its surface area, flow association, fabric conductivity, and the bodily houses of the fluids concerned.
Flow Arrangements and Efficiency
There are several approaches fluids can circulate thru a warmth exchanger: counterflow, parallel float, crossflow, or hybrid configurations. Counterflow systems tend to be the maximum green, as the recent and bloodless fluids circulate in opposite guidelines, keeping a greater temperature gradient throughout the whole unit.
Each association has implications for thermal performance, strain drop, and area necessities. Choosing the perfect configuration is key to optimizing the exchanger’s overall performance and minimizing power consumption in an business method.
Types of Heat Exchangers and Their Applications
Shell and Tube Heat Exchangers
Among the maximum commonplace and broadly used types, shell and tube warmth exchangers encompass multiple tubes enclosed in a cylindrical shell. One fluid flows within the tubes while the opposite moves over them, permitting big surface regions for heat switch. These exchangers are perfect for excessive-stress packages and are regularly utilized in strength era and oil refining.
The design permits easy cleaning and renovation, specially in dirty or scaling-inclined environments. Moreover, shell and tube fashions may be custom designed with one-of-a-kind baffle arrangements and tube configurations to match specific fluid dynamics.
Plate Heat Exchangers
Plate heat exchangers use skinny, corrugated steel plates stacked together to create separate flow channels. Fluids trade between plates, bearing in mind efficient warmness transfer across a compact footprint. This layout enhances turbulence and improves thermal conductivity, making it appropriate for industries wherein area-saving and thermal precision are vital.
Common programs encompass HVAC systems, dairy processing, and pharmaceutical production, wherein cleanability and temperature manage are essential
Air Cooled Heat Exchangers
Air cooled warmth exchangers use ambient air rather than water to put off warmth from a technique fluid. These systems are specifically beneficial in regions in which water is scarce or steeply-priced. Fans power air over finned tubes, permitting warmness switch without counting on outside water resources.
They are commonly utilized in energy plants, herbal fuel centers, and petrochemical web sites, in which environmental issues and water conservation are key operational worries.
Double Pipe and Spiral Heat Exchangers
Double pipe exchangers are designed for small-scale packages, using concentric pipes to switch warmness among two fluids. They offer simplicity and simplicity of protection, but are much less green for big-quantity or high-stress structures.
Spiral warmth exchangers, alternatively, use coiled channels to encourage a self-cleansing, high-performance float direction. These are frequently used for slurries, viscous fluids, or procedures involving solids, thanks to their resistance to fouling and clogging.
Material Selection and Corrosion Resistance
Importance of Choosing the Right Materials
The durability and effectiveness of a warmness exchanger are heavily stimulated by way of the substances used in its creation. Stainless metallic, titanium, copper alloys, and nickel-primarily based substances are regularly selected based totally on their thermal conductivity and corrosion resistance. Aggressive fluids, severe temperatures, and excessive pressures all necessitate careful material consideration.
Material compatibility with the fluids worried helps lessen scaling, pitting, and cracking. Selecting the best alloy no longer simplest extends the existence of the warmth exchanger but also minimizes downtime because of leaks or contamination.
Coatings and Surface Treatments
In addition to cloth choice, specialized coatings and floor treatments can similarly protect warmth exchangers from corrosive environments. Techniques like anodizing, passivation, and epoxy coating offer additional obstacles that prolong system existence and reduce upkeep periods.
Advanced production techniques now allow for advanced surface finishes that withstand biofilm formation and scaling, specifically crucial in food processing and pharmaceutical applications.
Designing for Efficiency and Sustainability
Maximizing Thermal Transfer
Efficiency is a number one situation in warmth exchanger layout. Engineers purpose to increase the floor place for thermal contact even as retaining plausible flow resistance. Enhancing turbulence thru floor geometry or float sample optimization can significantly enhance heat switch quotes without requiring more area.
Compact designs are favored now not best for saving space however also for decreasing fabric fees and minimizing thermal losses. This makes the warmth exchanger a key contributor to normal energy control in contemporary business systems.
Reducing Environmental Impact
In nowadays’s regulatory surroundings, minimizing carbon footprints and meeting sustainability goals are essential. Heat exchangers make contributions to these efforts with the aid of recovering waste heat that might otherwise be lost, as a consequence enhancing energy utilization throughout a facility.
By lowering the need for extra heating or cooling enter, warmness exchangers play an immediate role in decreasing emissions and maintaining assets. Innovations together with hybrid structures and renewable-powered exchangers further integrate thermal management into sustainable development strategies.
Maintenance and Operational Reliability
Preventive Maintenance Practices
Regular protection is essential to preserving the performance and reliability of a warmness exchanger. Over time, scaling, fouling, and corrosion can degrade overall performance. Monitoring temperature differentials, pressure drops, and drift prices can provide early warnings of inefficiencies.
Preventive renovation routines, consisting of periodic cleaning, inspection, and strain testing, assist avoid sudden disasters. For excessive-value processes, predictive protection the use of IoT sensors and virtual diagnostics is increasingly more being followed to forecast device situation and provider desires.
Downtime Minimization and Safety
A failure in a warmness exchanger can lead to procedure shutdowns, product losses, or even protection risks. Therefore, operational reliability is a layout precedence. Using gasketed connections, modular plate assemblies, or without problems on hand tube bundles lets in for short maintenance and element replacements.
Safety systems together with strain alleviation valves and temperature video display units make sure that the exchanger operates inside desirable limits, reducing the danger of overpressure or overheating activities.
The Role of Innovation in Heat Exchanger Technology
Digital Integration and Smart Monitoring
The upward push of smart factories and facts-driven preservation has brought virtual transformation to warmth exchanger operations. Integrated sensors can constantly monitor fluid temperatures, flow prices, and vibration degrees, transmitting real-time records to valuable manage structures.
This digital layer enables predictive analytics and faraway troubleshooting, decreasing manual intervention and improving gadget visibility. It additionally lets in operators to optimize overall performance dynamically based on varying manner situations.
Customization and Modular Systems
Modern warmness exchanger systems are regularly designed with modularity in mind, permitting plants to scale or adapt equipment to evolving production demands. Customizable layouts, removable additives, and multi-characteristic talents permit more flexibility throughout business applications.
The collaborative efforts of engineers and equipment designers, regularly operating intently with an commercial merchandise manufacturer, make it viable to create gadgets tailored to highly particular wishes, from high-viscosity chemical strategies to cryogenic applications.
Future Trends in Heat Exchanger Development
Emphasis on Compactness and Versatility
The destiny of heat exchanger design lies in maximizing performance inside increasingly restricted area. As commercial systems become more incorporated, the call for for compact yet effective warmth exchangers will retain to upward thrust. Research into microchannel and nano-stronger surfaces is paving the manner for extra powerful and area-efficient solutions.
Materials science can even play a valuable function, with newer alloys and composites providing better thermal houses and corrosion resistance at decreased costs.
Sustainability and Circular Economy Integration
The pass toward circular economy concepts will affect how warmth exchangers are synthetic, used, and recycled. Designs will more and more include recyclable materials, longer service lives, and strength-green production strategies. Lifecycle tests and carbon accounting becomes key metrics for evaluating thermal systems.
Energy recuperation solutions using heat exchangers will become a vital approach for industries trying to meet emission reduction objectives and electricity efficiency benchmarks, in particular in energy-in depth sectors.
Conclusion
Heat exchangers are necessary in a extensive range of business programs, making sure superior thermal law, strength conservation, and system reliability. As technologies evolve and industries prioritize sustainability and efficiency, warmth exchangers will continue to play a valuable function in shaping the destiny of commercial operations.
With developing demand for high-performance, compact, and customizable answers, current thermal structures are more and more being designed with both engineering precision and environmental duty in mind. In this panorama, the partnership with an experienced industrial product manufacturer remains vital for turning in sturdy, efficient, and future-ready thermal answers.
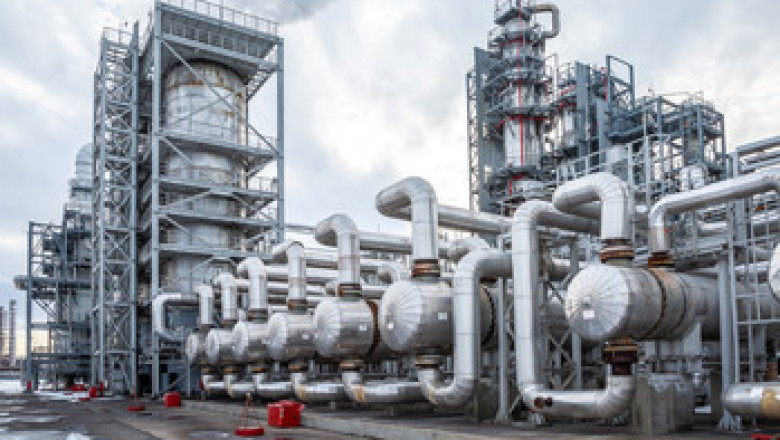

Comments
0 comment