views
Using the PDCA Cycle in Manufacturing A Practical Approach
The PDCA cycle—Plan, Do, Check, Act—is a undying approach for non-stop development, deeply rooted in fine management and operational excellence. While it was at the start introduced by means of Dr. W. Edwards Deming and adapted from the Shewhart cycle, its relevance these days remains powerful, in particular in the production sector. The PDCA cycle helps sustainable development, process optimization, and facts-driven selection-making.
This article explores how the PDCA cycle may be nearly implemented in production settings, gives actionable strategies for implementation, identifies commonplace pitfalls to avoid, and especially connects the concept to broader areas which includes undertaking management and educational assist (like animation task help and cheap mission assist) for the ones analyzing industrial engineering, enterprise management, or operations control.
Understanding the PDCA Cycle: A Quick Recap
Before diving into actual-international software, it's important to comprehend what each degree of the PDCA cycle includes:
1. Plan
Identify a problem or opportunity for improvement. Analyze the present day process, accumulate applicable facts, and set measurable targets.
2. Do
Implement the deliberate answer on a small scale. This could be a pilot run or a prototype phase.
3. Check
Evaluate the outcomes of the motion taken. Was there improvement? Are there unexpected consequences? Analyze data collected in the course of the Do section.
4. Act
If the solution changed into successful, standardize the brand new technique and put into effect it company-wide. If now not, revisit the plan and start the cycle once more.
This iterative system guarantees continuous refinement and adaptation, middle principles in current manufacturing.
Why the PDCA Cycle Works in Manufacturing
Manufacturing is a discipline that flourishes on precision, performance, and consistency. The PDCA cycle offers a framework for iterative problem-fixing, that is critical in regions together with:
- Quality control
- Process standardization
- Lean production
- Equipment maintenance
- Safety protocols
- Waste reduction (aligned with Six Sigma and Kaizen methodologies)
Whether you are walking a small fabrication keep or managing a global production line, the PDCA approach offers a scalable version to enhance overall performance with out disrupting ongoing operations.
Real-World Applications of the PDCA Cycle in Manufacturing
Let’s explore how each degree of the PDCA cycle may be almost implemented inside a regular manufacturing context:
Plan: Identifying Inefficiencies and Opportunities
In this initial segment, the point of interest is on figuring out inefficiencies. For example, a bottleneck inside the meeting line that will increase lead instances can be pinpointed. Managers might also:
- Use gear like Value Stream Mapping (VSM) or Root Cause Analysis
- Conduct employee interviews
- Review operational information from ERP structures
At this degree, clear and measurable goals are set. For example, "Reduce system downtime by way of 10% within three months."
Do: Implementing Pilot Solutions
Once a method is described, it should be examined on a small scale:
- Adjust one manufacturing shift
- Change provider scheduling for one product line
- Introduce predictive protection software program on one machine
This helps reduce risk while testing feasibility.
Check: Monitoring and Analysis
Using records analytics, supervisors and engineers evaluate whether the pilot resulted in improvement:
- Compare output facts pre- and publish-implementation
- Review incident reviews or downtime logs
- Solicit comments from floor body of workers
Statistical Process Control (SPC) charts and Key Performance Indicators (KPIs) assist determine fulfillment or screen the need for adjustments.
Act: Standardize or Rework
If results are high quality, the procedure is standardized throughout different devices or departments. If not, insights gained are used to refine the technique and re-enter the cycle. Documentation and training play a key role within the "Act" section to ensure consistency.
Case Study: Using PDCA to Reduce Waste in a Packaging Plant
Problem: A mid-sized food packaging enterprise noticed a full-size growth in packaging fabric waste.
Plan: Management carried out a root cause evaluation and recognized inconsistency in machine calibration because the wrongdoer. The purpose turned into to reduce material waste through 15% in ninety days.
Do: They recalibrated one line of packaging machines and trained one group on new processes.
Check: Over the subsequent month, they measured the amount of packaging waste and discovered a 12% reduction.
Act: The employer rolled out recalibration throughout all packaging strains and instituted monthly training updates. Waste became ultimately decreased with the aid of 18%.
The PDCA Cycle Beyond Manufacturing: Academic Relevance
The PDCA framework isn’t just for industrial use; it’s extensively followed in academic disciplines like project control, best warranty, and business strategy. For students juggling technical topics like operations or supply chain control, making use of the PDCA methodology in assignments can help them stand out.
This is where cheap assignment help and animation assignment help services can play a supportive role:
Cheap Assignment Help: Many students are under pressure to meet closing dates, recognize complex topics, and stability part-time paintings. Affordable academic offerings can help with growing dependent, logical assignments using fashions like PDCA.
Animation Assignment Help: For those in multimedia or layout courses, PDCA can manual assignment improvement from concept to execution. Professionals can assist visualize the Plan and Do levels via storyboards and prototypes, Check the use of target market remarks, and Act through final edits and transport.
Using PDCA in academic projects now not best improves best but additionally aligns with real-global questioning a talent employers deeply fee.
Common Mistakes When Implementing PDCA in Manufacturing
While the PDCA cycle is simple in idea, terrible implementation can undermine its capability. Here are commonplace pitfalls:
1. Skipping the Planning Phase
Jumping into solutions with out proper records gathering often ends in temporary fixes in place of long-time period improvements.
2. Lack of Measurable Objectives
Without clean KPIs, it’s impossible to determine if a alternate became a hit.
3. Poor Communication
Teams ignorant of what changes are being examined or why are not likely to observe new techniques.
4. Inconsistent Monitoring
Data series have to be rigorous and continuous to appropriately evaluate modifications.
5. Failure to Standardize Successful Changes
Even whilst a solution works, it is able to not be institutionalized because of lack of documentation or training.
Best Practices for PDCA Success in Manufacturing
1.Involve Cross-Functional Teams
From gadget operators to first-rate manipulate team of workers, concerning multiple departments guarantees broader perception.
2.Use Visual Management Tools
Kanban boards, dashboards, and SPC charts make it easier to track and speak progress.
3.Maintain a PDCA Logbook
Documenting every cycle helps in learning from each successes and screw ups.
4.Combine with Other Methodologies
PDCA works properly alongside Lean, Six Sigma, and Total Quality Management (TQM) standards.
5.Encourage a Culture of Continuous Improvement
The PDCA cycle isn't a one-time event. Foster a mind-set that embraces alternate and remarks.
Conclusion
The PDCA cycle is extra than a theoretical model it is a hands-on, iterative approach that empowers manufacturing groups to solve issues methodically and sustainably. By integrating planning, motion, evaluation, and refinement into each day operations, corporations can increase productivity, improve exceptional, and reply correctly to trade.
Moreover, the versatility of the PDCA cycle extends beyond the shop floor. Whether you're a student seeking animation assignment help for a multimedia project or exploring cheap assignment help for an industrial engineering case study, applying PDCA principles can elevate the clarity and impact of your work.
As industries evolve and customer expectancies grow, manufacturers who master continuous development via the PDCA cycle will be the ones who lead, innovate, and prevail.
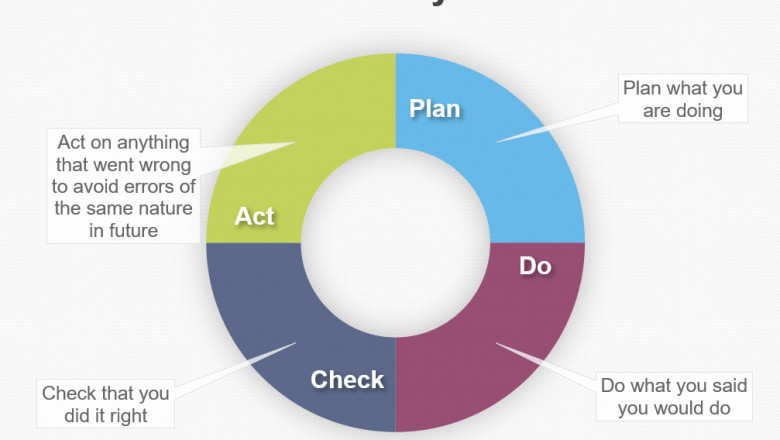

Comments
0 comment